Recent days have witnessed the rapid development of intelligent packaging and active packaging in the food sector, which has increased people's concerns. However, a lot of people get confused between these two types of technology. Therefore, the difference between intelligent packaging and active packaging will be clarified based on the published scientific literature in this writing.
Intelligent Packaging
Intelligent packaging is capable of informing the consumer, or others within the food supply chain, about the state of the food or the environment that the food has been kept in. For example, some forms of intelligent packing incorporate a sticker that changes colour if the product is kept above or below critical temperatures, as this could indicate it might be unsafe for consumption. Researchers are also investigating indicators that detect different aspects of food quality as these could potentially replace use-by dates. Having more dynamic use-by dates could help improve food safety and reduce food waste.
Microbiological and chemical tests of the products are regularly performed at the company level during production and before delivery. But in most cases there is no such control after delivery to the supermarket. Intelligent packaging will close this gap as they are able to monitor and display the quality status from the point of manufacture up to the customer. This permanent monitoring not only minimizes unnecessary food waste but also protects consumers against potential food poisoning, maximizes the efficiency of the food industries, and improves traceability.
In general there are three main technologies which are used for intelligent packaging systems: data carriers, indicators, and sensors.
    |
Fig. 2. Active agents for active food packaging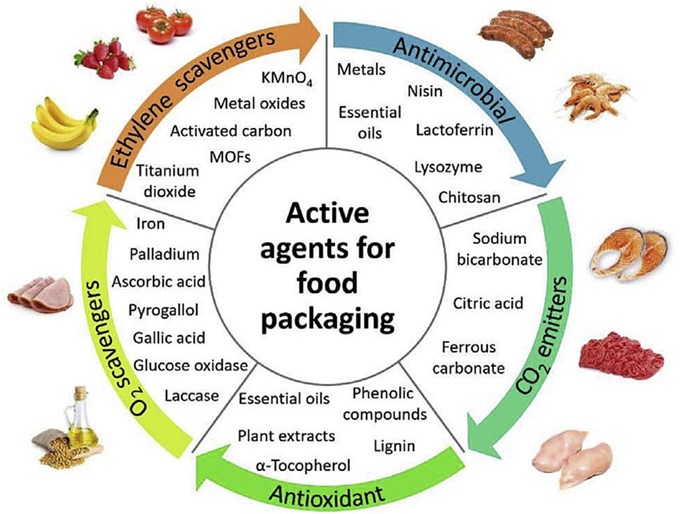 |
Fig. 1. Active agents for active food packaging |
+ Data carriers
Data carriers help to make the information flow within the supply chain more efficient. The function of data carriers is not to monitor the quality of the products, but to guarantee traceability, automatization, theft protection, or counterfeit protection. To ensure this, data carriers store and transmit information about storage, distribution, and other parameters. Therefore, they are often placed on tertiary packaging. The most frequently used data carriers are barcode labels and RFID (Radio Frequency Identification) tags.
+ Indicators
Indicators determine the presence or absence of a substance, the extent of a reaction between different substances or the concentration of a particular substance. This information is visualized by direct changes, e.g., different color intensities. Depending on the indicator they are placed inside or outside of the package. Examples are time temperature indicators, freshness indicators, gas indicators.
+ Sensors
There are different types of sensors that investigate different parameters, for instance the gas sensors. The progress of spoilage can be determined by the concentration of certain gases, like CO2 or H2S. The gas sensors make use of these properties by monitoring them. Those respond quantitatively and reversibly to the presence of a gas by changing the physical parameters of the sensor. Biosensors have a receptor made of biological materials such as enzymes, antigens, hormones, or nucleic acids. Depending on the measuring parameters, the transducer can be electrochemical, optical, acoustic, etc.
    |
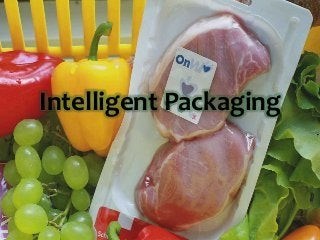 |
Fig. 2. Intelligent packaging |
Active packaging
Active packaging is a solution, in which the packaging, the product, and the environment interact. These are the systems, which (as a result of the chemical, physical, and biological activities) actively change conditions of the packed food, cause an extension of its sustainability and thus its shelf life, and guarantee or significantly improve the microbiological safety and/or sensory properties, while maintaining its quality.
In contrast to the traditional packaging materials, active packaging causes extending the shelf life of food and preserving its higher quality during reactions with the internal atmosphere and the product.
Active packaging is designed either as an active layer incorporated onto traditional packaging material or as sachets containing active compounds, that are included inside the packaging. The following active packaging systems are used in the food industry:
• oxygen, carbon dioxide, and ethylene scavengers
• carbon dioxide emitters
• odor emitters and absorbers
• relative humidity regulators (water content in the packaging atmosphere)
• antibacterial substances
• antioxidants
The largest group of emitters consists of antimicrobial substances for use inside packaging. These substances may be added to packaging in different forms such as:
• sachets or mats with volatile antimicrobial compounds
• active substances embedded in the polymer structure
• active substances applied to the polymer surface
• active substances immobilized on the polymer using ionic and covalent bonds
• packaging films, which have antimicrobial properties (e.g., films based on chitosan)
• edible food coatings
In short, as packing technology has become more advanced, active packaging has been developed which is capable of performing additional functions such as: decreasing microbial growth; extending shelf life, and, retaining food quality by preventing undesirable flavours or colour changes from developing, or nutrients from being lost. Intelligent packaging, on the other hand, monitors the state of the food within the packaging or surrounding environment and relays this information to the food processor, retailer or consumer.
References
Ahmed, I., Lin, H., Zou, L., Li, Z., Brody, A.L., Qazi, I.M., Lv, L., Pavase, T.R., Khan, M.U., Khan, S., et al. (2018). An overview of smart packaging technologies for monitoring safety and quality of meat and meat products. Packag. Technol. Sci. 31, 449–471.
Carla Vilela et al. (2018). A concise guide to active agents for active food packaging. Trends in Food Science & Technology 80:212-222.
Ghaani, M.; Cozzolino, C.A.; Castelli, G.; Farris, S. (2016). An overview of the intelligent packaging technologies in the food sector. Trends Food Sci. Technol. 51, 1–11.
McFarlane, D.; Sheffi, Y. (2003). The impact of automatic identification on supply chain operations. Int. J. Logist. Manag. 14, 1–17.
Patricia Müller and Markus Schmid (2019). Intelligent Packaging in the Food Sector: A Brief Overview. Foods, 8, 16.
Poyatos-Racionero, E.; Ros-Lis, J.V.; Vivancos, J.-L.; Martines-Manez, R. (2018). Recent advances on intelligent packaging as tools to reduce food waste. J. Clean. Prod. 172, 3398–3409.
Sohail, M.; Sun, D.-W.; Zhu, Z. (2018). Recent developments in intelligent packaging for enhancing food quality and safety. Crit. Rev. Food Sci. Nutr. 1–13.
Wyrwa J., Barska A. (2017). Innovations in the food packaging market: active packaging. Eur Food Res Technol. 243:1681–1692.
Thang Nguyen Trong
Faculty of Food Science and Technology